PCB PCB surface treatment commonly used with lead tin spray, lead-free tin spray, sink gold or OSP.
1. hot air leveling
Also known as hot air solder leveling, it is a process of coating molten tin-lead solder on the surface of PCB and heating compressed air leveling (blowing), so as to form a layer of copper oxidation resistance, but also provide good solderability coating. During hot air, copper tin intermetallic compounds are formed at the junction of solder and copper. The thickness of solder for protecting copper surface is about 1-2mil. PCB is immersed in molten solder during hot air leveling; the air knife blows the liquid solder before solidification; and the wind knife minimizes the meniscus of solder on the copper surface and prevents the solder from bridging. Hot air leveling can be divided into vertical type and horizontal type. It is generally considered that horizontal type is better. The main reason is that the coating of horizontal hot air leveling is more uniform, which can realize automatic production. The general process of hot air leveling process is micro etching, preheating, coating flux, tin spraying and cleaning.
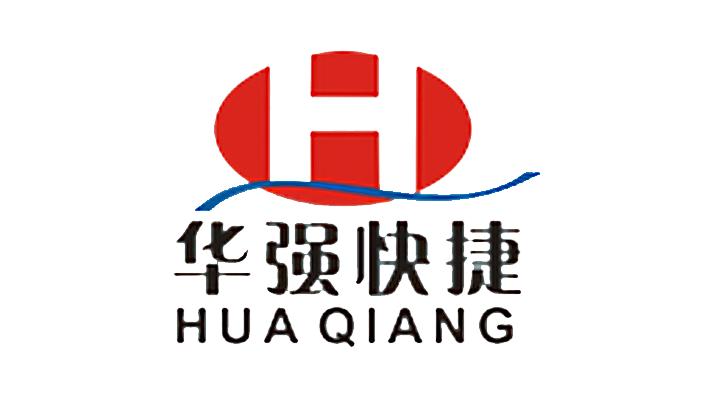
2. Organic coating is estimated to be used in about 25-30% of PCBs at present, and the proportion has been increasing (it is likely that organic coating is now in the first place over hot air leveling). Organic coating process can be used in low-tech PCB, also can be used in high-tech PCB, such as single-sided television PCB, high-density chip packaging board. For BGA, organic coating applications are also more. Organic coating is the most ideal surface treatment process for PCB without functional requirements for surface bonding or storage life limitations.
3. electroless nickel plating / leaching gold
Electroless nickel plating/gold dipping process is not as simple as organic coating. Electroless nickel plating/gold dipping seems to wear thick armor on PCB. In addition, electroless nickel plating/gold dipping process is not like organic coating as rust barrier, it can be useful in the long-term use of PCB and achieve good electrical performance. Therefore, electroless nickel plating / gold immersion is to wrap a thick layer of nickel-gold alloy on the copper surface, which can protect the PCB for a long time, and it also has the environmental tolerance that other surface treatment processes do not have. The reason for nickel plating is that gold and copper diffuse each other, and the nickel layer prevents the diffusion between gold and copper; without the nickel layer, gold will diffuse into copper within hours. Another advantage of electroless nickel/gold dipping is the strength of nickel, which limits the Z-direction expansion at elevated temperatures by only 5 microns thick. In addition, electroless nickel plating / immersion gold can also prevent copper dissolution, which will be beneficial to lead-free assembly. The general process of electroless nickel plating / gold leaching is acidic cleaning micro-corrosion pre-impregnation activation electroless nickel plating chemical gold leaching. There are mainly six chemical bath, involving nearly 100 chemicals, so the process control is difficult.
4. Silver dipping is cheaper than electroless nickel/gold dipping. If PCB has functional requirements and needs to reduce costs, silver dipping is a good choice. In addition to good flatness and contact of silver dipping, silver dipping process should be chosen. There are many applications of silver impregnation in communication products, automobiles, computer peripherals, and in high-speed signal design. It can also be used in high-frequency signals because of its excellent electrical properties unmatched by other surface treatments. EMS recommends the use of immersion silver technology because it is easy to assemble and has good inspection ability. However, due to defects such as loss of luster and voids in solder joints, the growth of silver impregnation is slow (but not decreased). It is estimated that at present, about 10%-15% of PCB uses the silver immersion process.
5. soaking tin
Since all solders are currently tin-based, the tin layer can match any type of solder. From this point of view, tin leaching technology has great prospects for development. However, tin whisker appeared in PCB after tin immersion process, and the migration of tin whisker and tin during welding process will bring reliability problems, so the use of tin immersion process is limited. Later, organic additives were added to the tin dipping solution to make the tin layer structure granular, which overcomes the previous problems and has good thermal stability and solderability. Tin dipping can form flat copper-tin intermetallics, which make tin dipping as solderable as hot air leveling without the headache of flatness; tin dipping also has no diffusion problem between electroless nickel/gold-dipping metals - copper-tin intermetallics can be firmly combined in one. Get up. Tin plate should not be stored for too long. Where is the future of PCB surface treatment technology, and it can not be accurately predicted. In any case, to meet customer requirements and protect the environment must first do!